Grasping Welding WPS Specifications: Ideal Practices and Techniques for High Quality Welds
In the world of welding, understanding Welding Treatment Specification (WPS) criteria is an important component that directly influences the high quality and stability of welds. Complying with these requirements guarantees uniformity and reliability in welding end results. Nevertheless, attaining quality in welds exceeds merely comprehending the standards; it involves implementing best practices and strategies that boost the craft to a level of precision and ability that distinguishes the average from the phenomenal. As we browse with the ins and outs of welding WPS criteria, discovering essential insights and approaches for achieving top-tier welds will be extremely important for welders looking for to stand out in their craft and produce welds that stand the test of time.
Understanding Welding WPS Requirements
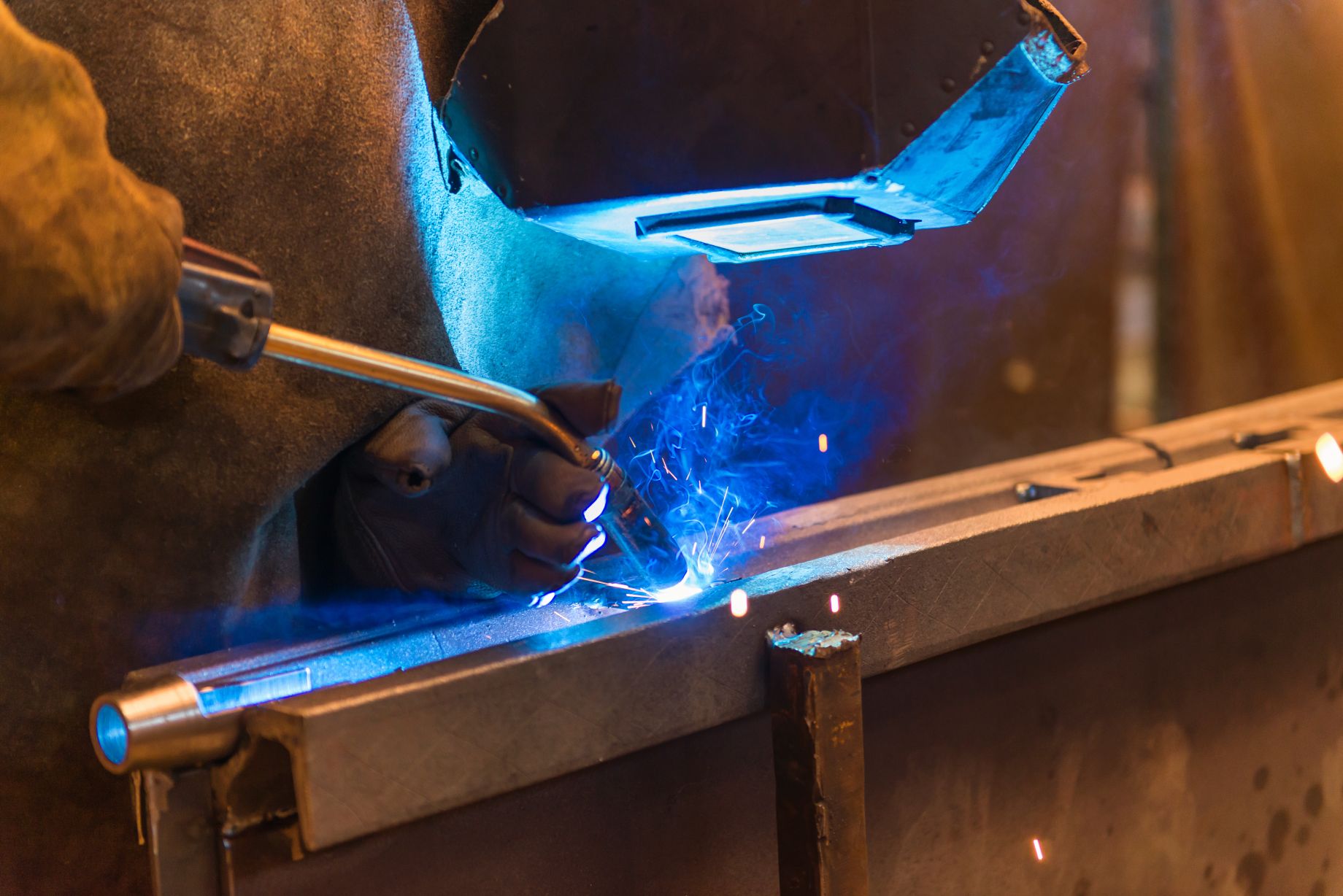
Recognizing WPS requirements is important for welders, inspectors, and engineers associated with welding procedures. By complying with WPS standards, welders can produce welds that fulfill the required mechanical properties and architectural honesty. Assessors depend on WPS paperwork to validate that welding procedures are being complied with properly which the resulting welds are of top quality. Engineers make use of WPS criteria to create welding treatments that ensure the durability and reliability of welded structures.
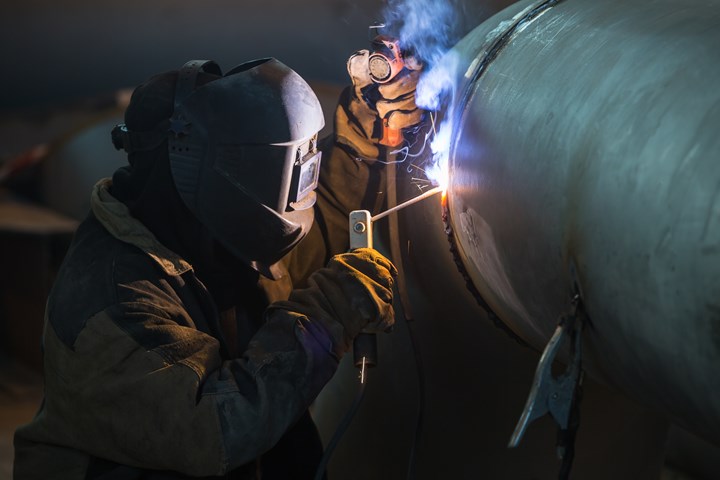

Essential Tools for Quality Welds
Understanding welding WPS criteria is essential for welders to effectively use the necessary tools needed for generating top quality welds. The kind of welding maker needed depends on the welding process being made use of, such as MIG, TIG, or stick welding. Wire brushes and breaking hammers are vital for cleaning the weld joint before and after welding to get rid of any type of pollutants that might influence the quality of the weld.
Trick Techniques for Welding Success
To accomplish welding success, one need to master the key strategies necessary for producing top notch welds. One important method is preserving the right arc length. Maintaining the electrode at the optimal range from the work surface is vital for developing strong, uniform welds. Furthermore, controlling the travel rate is vital. Relocating too promptly can result in not enough infiltration, while relocating also slowly can result in too much heat input and prospective defects. Appropriate adjustment of the electrode angle is one more official statement vital strategy. The angle at which the electrode is held can affect the bead form and infiltration of the weld. Additionally, ensuring constant gun angle and direction of traveling is important for uniformity in the weld grain. Lastly, preserving a steady welding and a stable hand setting throughout the procedure is crucial to accomplishing accuracy and uniformity in the welds. By mastering these key methods, welders can raise the high quality of their work and accomplish welding success.
Ensuring Conformity With WPS Standards
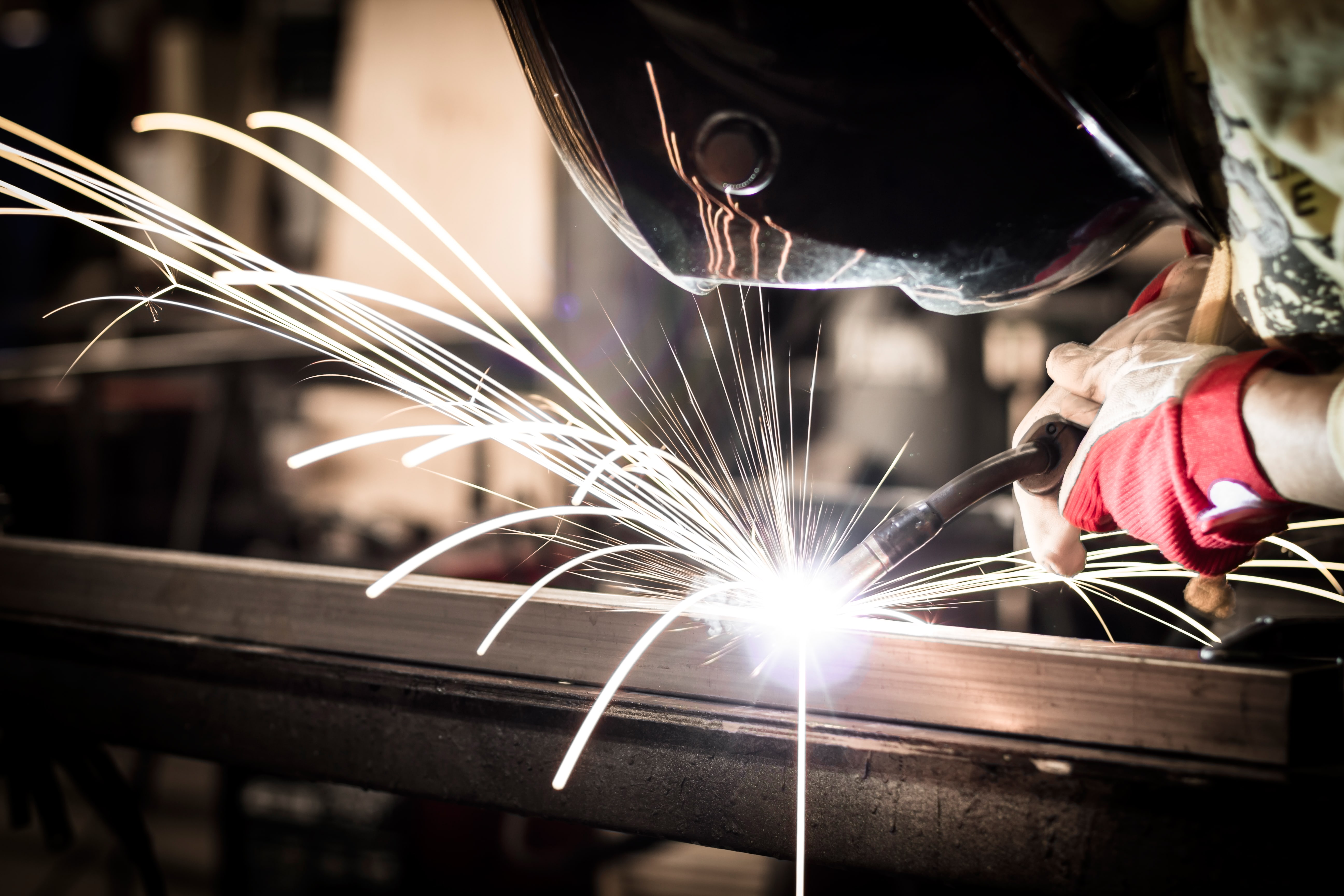
Furthermore, welders should undergo training to familiarize themselves with the WPS standards appropriate to their work. Regular audits and evaluations must be carried out to validate that welding activities straighten with the suggested WPS standards. Furthermore, keeping comprehensive records of welding criteria, equipment calibration, and assessment results is crucial for demonstrating compliance with WPS requirements - welding WPS. By carefully sticking to WPS standards, welders can make sure that their job satisfies the required high quality levels and adds to the total success of the welding task.
Troubleshooting Common Welding Issues
To address this, ensuring go to my site proper cleansing of the base metal before welding and using the correct protecting gas can substantially decrease porosity. Furthermore, distortion, splitting, and spatter are common welding difficulties that can be alleviated via proper joint prep work, regular warm control, and choosing the proper welding consumables. By extensively comprehending these common welding issues and their root triggers, welders can successfully repair problems and achieve top notch welds.
Final Thought
In conclusion, mastering welding WPS standards calls for a thorough understanding of the guidelines, utilizing essential tools, and applying key strategies for successful welds. Making sure compliance with WPS standards is important for producing high quality welds and avoiding common welding problems. By complying with best strategies and techniques, welders can accomplish regular and trusted cause their welding projects.
In the world of welding, mastering Welding Procedure Specification (WPS) requirements is a crucial component that directly influences the high quality and stability of welds.When diving into the world of welding methods, an essential element to comprehend is the value and intricacies of Welding Procedure Requirements (WPS) requirements. WPS requirements give a thorough guideline for welding procedures, ensuring consistency, high quality, and security in the welding process. The kind of welding equipment required original site depends on the welding procedure being used, such as MIG, TIG, or stick welding.Attaining welding success through the proficiency of key methods requires a comprehensive understanding and adherence to Welding Procedure Requirements (WPS) criteria.